CASE STUDY REF#17
THE CHALLENGE
Increase ROA for North American plant
An European FMCG company partnered with our team to conduct a wall-to-wall review of one of their North American plants. The subsequent project’s objective was to increase ROA for the plant and demonstrate to the group the effectiveness of Lean Manufacturing Tools with a view to a roll out for their North American assets.
OUR FINDINGS
We identified six items for improvement:
- Traditional top-down culture with minimal operator involvement in problem-solving and continuous improvement disciplines
- Minimal visual management tools on the floor. KPIs only discussed weekly with Plant Manager and direct reports
- Poorly balanced packaging lines for key SKUs leading to a loss in direct labor productivity
- Low packaging machine up-time
- Yield for key production lines was regularly below both budget and engineering targets
- Poorly scheduled milk deliveries, poor allocation of SKUs based on the fat content of incoming milk
IMPLEMENTATION
We focused on 3 areas
of impact to optimize Lean Manufacturing Tools
Development and implementation of tailored management training for supervision and management. Setting targets and relevant KPIs, Short Interval Control and variance analysis, daily, weekly and monthly action log management.
Training in basic continuous improvement tools: Sources of waste, 5 Whys, RCA. Visual management workshops with operators (one Kaizen event implemented per production line).
Standard work analysis and work observation campaigns with supervisors, Takt time/ cycle time analysis by line, rebalancing and training by workstation.
Implementation of ‘Overall Asset Effectiveness’ on a key production line and identification of bad actors for maintenance.
Design and implementation of refined yield metrics (moisture, protein, fat, giveaway) and setting of targets based on FG SKUs and inputs.
Review of milk deliveries by supplier and implementation of supplier service ranking.
Design and implementation of refined yield metrics (moisture, protein, fat, giveaway) and setting of targets based on FG SKUs and inputs.
Review of milk deliveries by supplier and implementation of supplier service ranking.
RESULTS
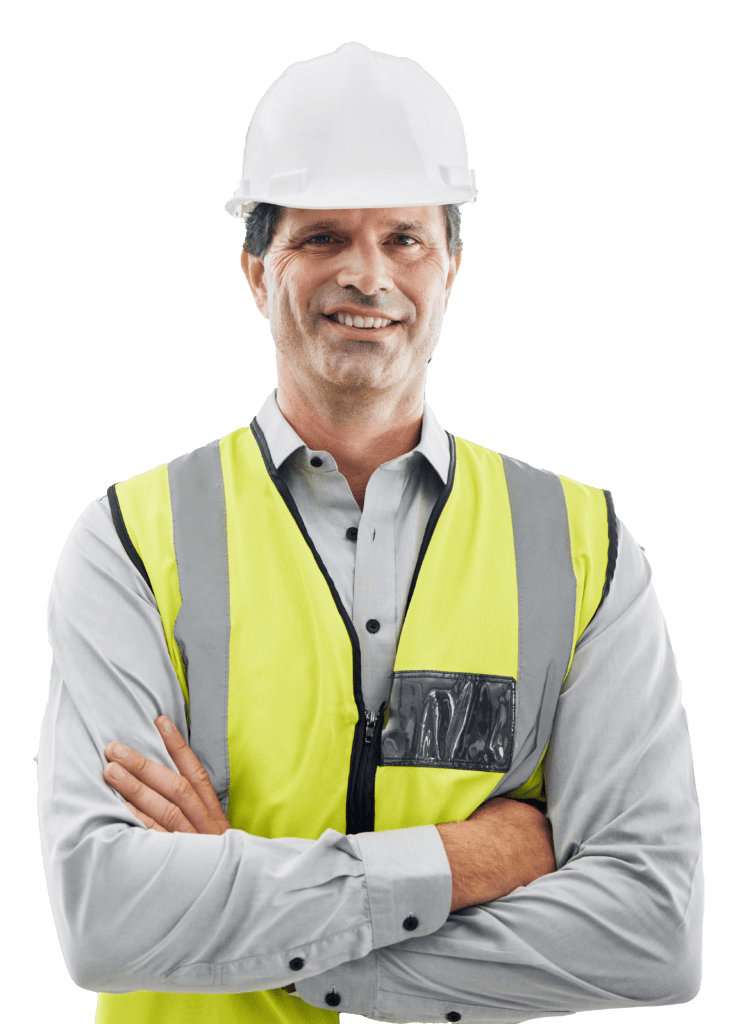
"Compared with the other consultants I have worked with in the past, I found that you really listened to what we had done in the past but had not been able to implement. Because of this, we were able to implement change faster and sustainably."
Plant Manager
CONTACT
Achieve similar outcomes
for your organization
Discuss how we can tailor solutions to your organization.