Case study REF#05
THE CHALLENGE
Severe limitations of training methods
An aging, retiring workforce, and the rapid influx of new hires exposed severe limitations of the on-the-job “buddy” training methods. This placed productivity, safety, and quality at risk. The organization needed a standardized methodology to develop operators, front line leaders rapidly, and managers to consistently execute standard operating procedures.
OUR FINDINGS
Identified six items for improvement
Each operating unit had evolved its home-grown knowledge transfer and training systems
Methods of performing the same job task varied from shift to shift and operator to operator
In some cases, there were no documented procedures for performing critical job tasks
Supervisors often did not understand the standard method for performing critical job tasks under their command
Active supervision levels were very low, driven largely by insecurity associated with not understanding standard procedures
The training process did not include a demonstration of competency or certification of trainers or trainees
IMPLEMENTATION
We focused on five areas of impact to improve standardized methodology
A 4-level Standard Work Methodology was developed, including Standard Work, Standard Day, Leader Standard Work, and Layered Audits, to streamline processes and ensure continuous improvement.
Standard Work was established to define the best method for job tasks, ensuring consistency and quality.
The sequencing of the implementation of Standard Work levels was based on operational needs, such as focusing on Standard Work for operations with a high influx of new hires or Leader Standard Work for those with inexperienced supervisors, to align with strategic goals.
Leader Standard Work Checklists were developed for supervisors, planners, schedulers, and managers to foster accountability and support active supervision and validation of standard work adherence.
Leader Standard Work Checklists for maintenance personnel, including supervisors, planners, schedulers, and managers, were created to ensure consistent and reliable operations for long-term success.
RESULTS
All delivered with the following benefits
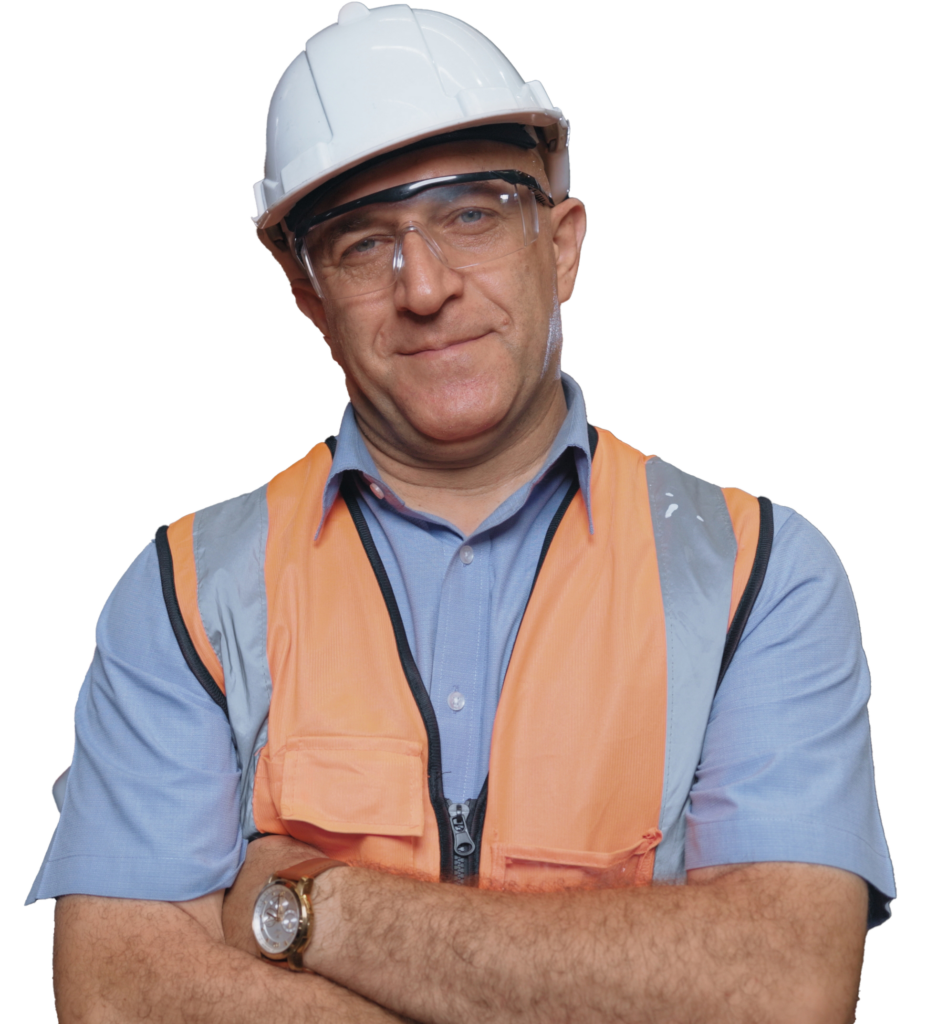
Standard Work allows us to flip the disadvantage of having a high percentage of our workforce retire into a competitive differentiator
Plant Manager
CONTACT
Achieve similar outcomes
for your organization
Discuss how we can tailor solutions to your organization.