Case study REF#19
THE CHALLENGE
Optimize production uplift in response to 23% C.A.G.R.
A North American Independent Oil & Gas Company faced with an aggressive long-range plan, based on 23% C.A.G.R. (compound annual growth rate), which would double production over five years. The client realized that this would present considerable challenges to the business as it was currently being operated, and asked ArMur for an analysis to identify key areas for improvement including production uplift, facility construction cycle time compression and permit throughput increase.
OUR FINDINGS
Identified six items for improvement
-
Organizational capabilities and capacities were not sufficient to achieve a 23%
volume CAGR commitment -
Planning across functions was not integrated, resulting in poor communications
and goal prioritization -
New Drill PoPs were well below L.R.P. requirements
-
Downtime and rate loss in base well production were not addressed promptly,
causing significant production loss -
Capital workovers were backlogged, and there was no clear prioritization method
-
Lack of stability in Supply Chain processes and methodologies meant high
material spend and frequent shortages
IMPLEMENTATION
We focused on 4 areas of impact
Designed and implemented a process-focused organization with clearly defined roles and responsibilities, creating improved decision making by creating accountability at all levels in the organization.
Linking long term planning to short term execution using joint, structured planning and review processes.
New Drill Readiness: Developed and installed clearly defined gate management processes and supporting documentation. Managers were then held accountable for their people achieving targets within agreed cycle times.
Production and Operations: Pumper routes were optimized, creating more field time to maximize intervention opportunities (downtime and rate losses) on wells. Created a Centralized Command Center for a proactive intervention approach to automated wells.
Capital Workovers: Redesigned the W/Over process to reduce rework cycle times, clearly define rig priorities, positively impacting base production.
Supply Chain / Facilities Construction: Implemented a modular battery design to improve demand predictability and forecasting to critical suppliers. Designed and installed clearer, simpler S.C.M. (Supply Chain Management) processes to improve performance.
RESULTS
All delivered with the following benefits
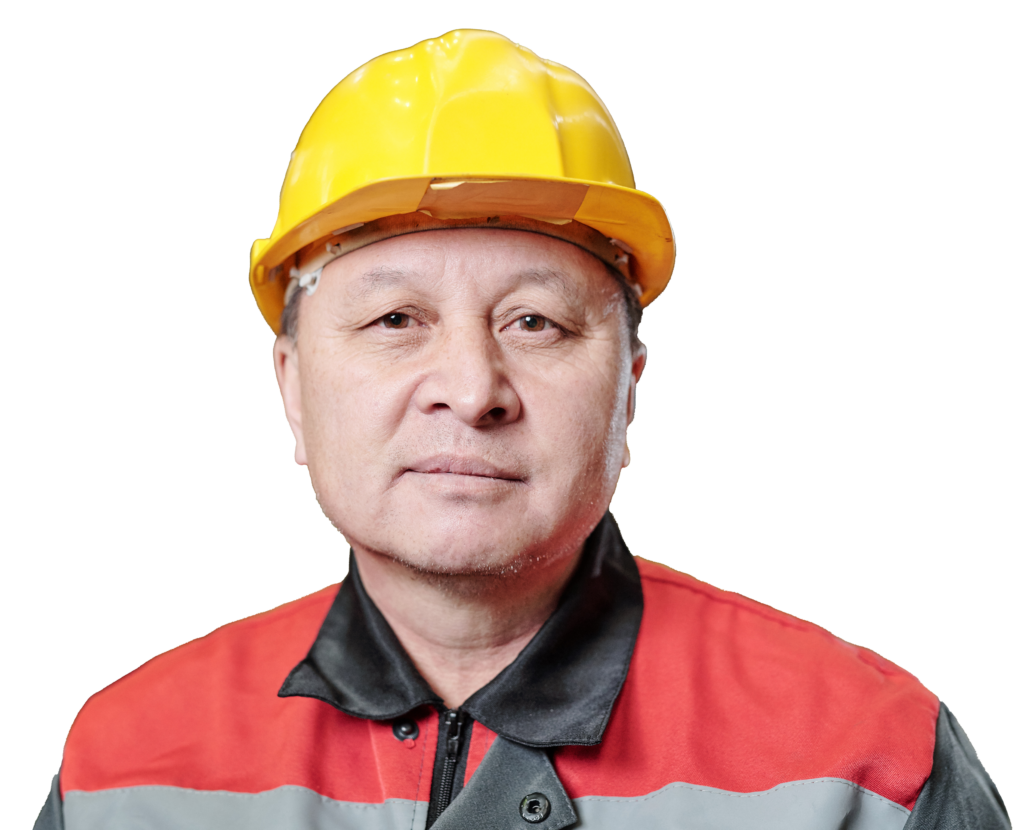
I didn’t need to spend six months training consultants. You guys know the industry and hit the ground running.
Operations Manager
CONTACT
Achieve similar outcomes
for your organization
Discuss how we can tailor solutions to your organization.